What is EDM?
A revolution in precision
Electrical discharge machining is a non-conventional process that uses electrical discharges to remove material from a workpiece. At Electroerosiones Navarra, we are experts in this innovative technique that offers unmatched precision and the ability to work with a wide variety of materials, including conductive metals and those of great hardness or difficult to process.
How does it work?
During the EDM process, a controlled electrical discharge generates extreme heat that melts and vaporizes the material in a precise manner. This targeted erosion makes it possible to create complex shapes and minute details with millimeter accuracy. It is also particularly effective for working with hard, resistant materials such as hardened steel or titanium.
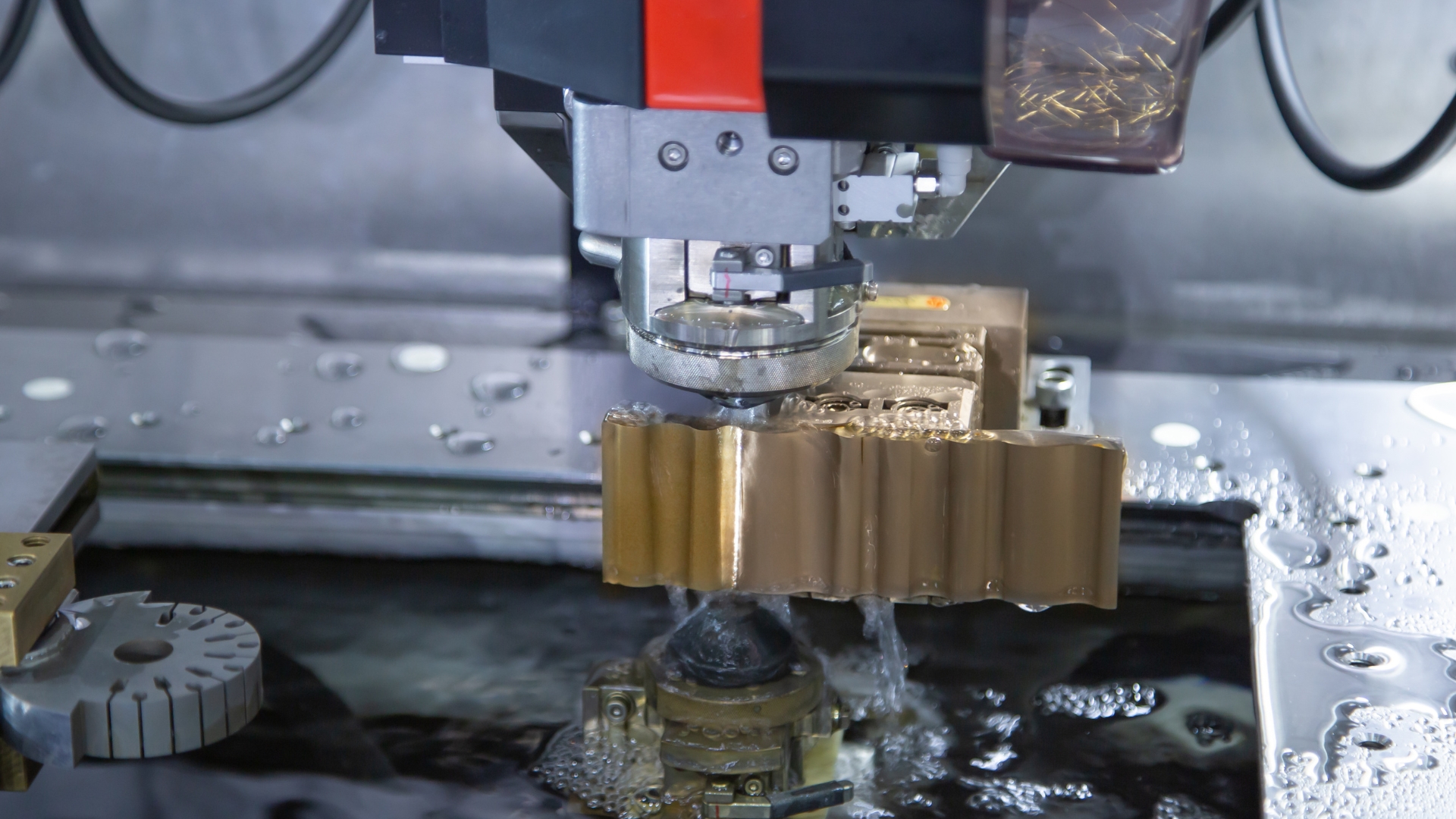
Types of EDM
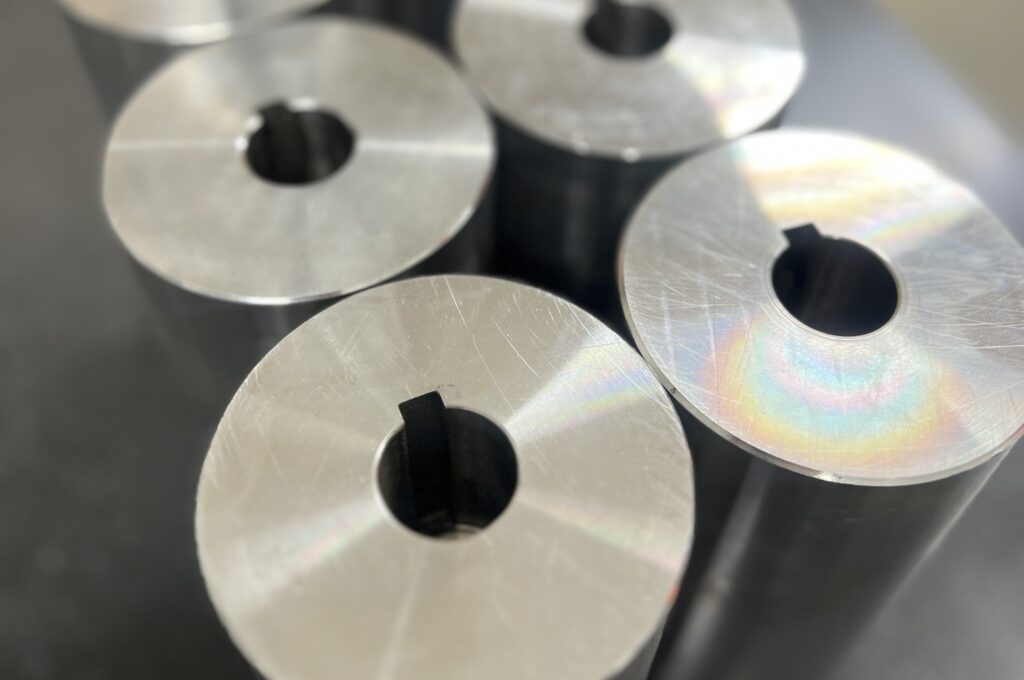
By penetration
Die sinking EDM uses a shaped copper or graphite electrode to erode conductive materials using controlled electrical discharges. This process allows complex shapes to be manufactured with high precision and high-quality finishes, making it ideal for hard materials or materials that are difficult to machine using conventional methods.
APPLICATIONS
- Manufacturing of molds and dies for plastic and metal.
- Production of dies and stamps for the automotive industry.
- Creation of customized medical parts.
- High precision engravings and cavities.
- Manufacturing of cutting tools and punches.
By thread
Wire EDM uses a conductive wire, usually of copper or brass among others, which moves through the workpiece to make extremely precise cuts. The electrically charged wire generates sparks that erode the material in a controlled manner, allowing for fine cuts and minute details. This process is ideal for creating complex shapes and high-precision work in hardened materials, such as pre-hardened dies or high-hardness metals.
APPLICATIONS
- Manufacturing of gears and precision parts
- Production of dies and matrices
- Cutting of aerospace components
- Medical industry: production of surgical instruments
- Manufacturing of moulds for plastic injection.
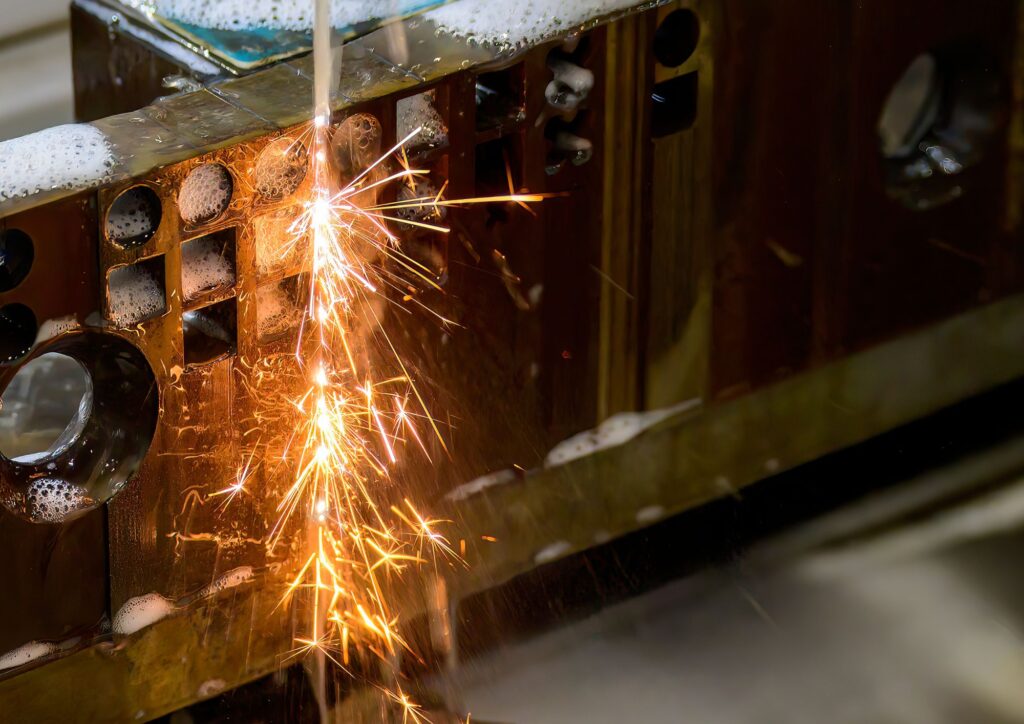
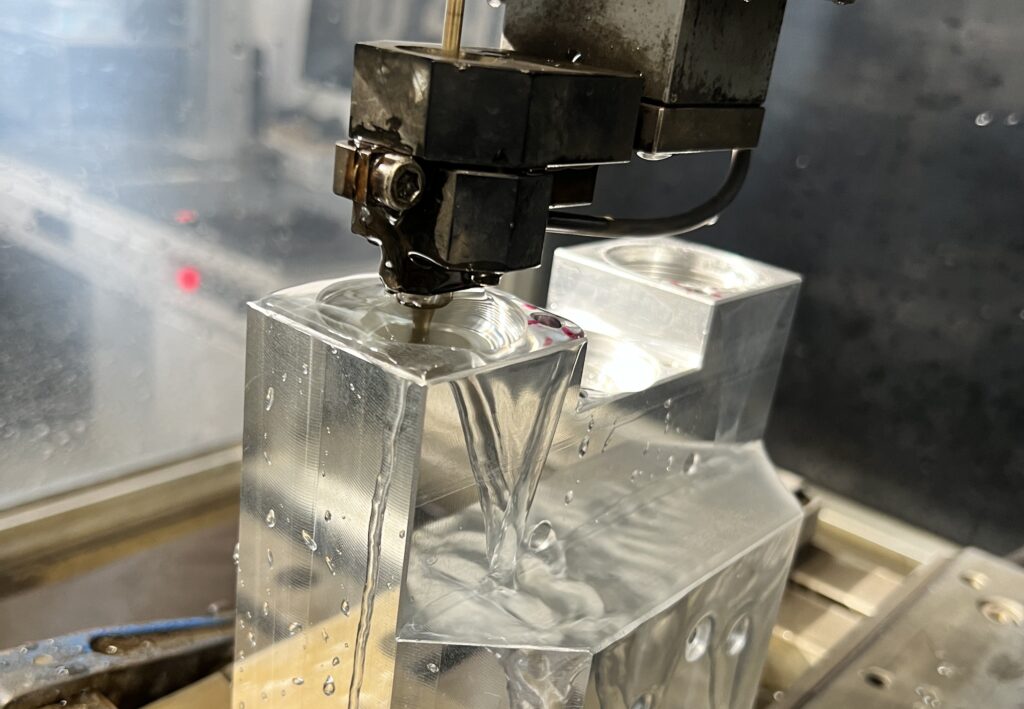
By drilling
Drilling EDM allows the creation of tiny, deep holes in conductive materials by means of controlled electrical discharges. Electrode tubes are used to achieve this, which facilitate the evacuation of the eroded material and the flow of the dielectric. This technique is essential for manufacturing complex interior shapes with high precision.
APPLICATIONS
- Manufacturing of medical and surgical tools.
- Production of aerospace components.
- Manufacturing of injection nozzles and ventilation holes in molds.
- Drilling cooling holes in turbines and micro-perforations in fuel injectors.
- Destruction of tools stuck in parts.
Advantages of EDM
Unparalleled precision
Electrical discharge machining allows the creation of parts with extremely tight tolerances and high quality surfaces.
Versatility
This technique is suitable for a wide variety of materials, from the softest to the hardest.
Efficiency
The ability to machine complex shapes in a single operation saves time and reduces production costs.
Minimum thermal impact
Because the process does not require physical contact, overheating and distortion of the workpiece is avoided.
do not hesitate to contact us.
We are here to help you achieve your manufacturing goals with maximum precision and efficiency.