Electroerosion: Precise Work
The Electroerosion It is a machining technique that has transformed the manufacturing industry, allowing for precise and efficient work with difficult-to-cut materials. Below, we will explore the history of EDM and its various uses today.
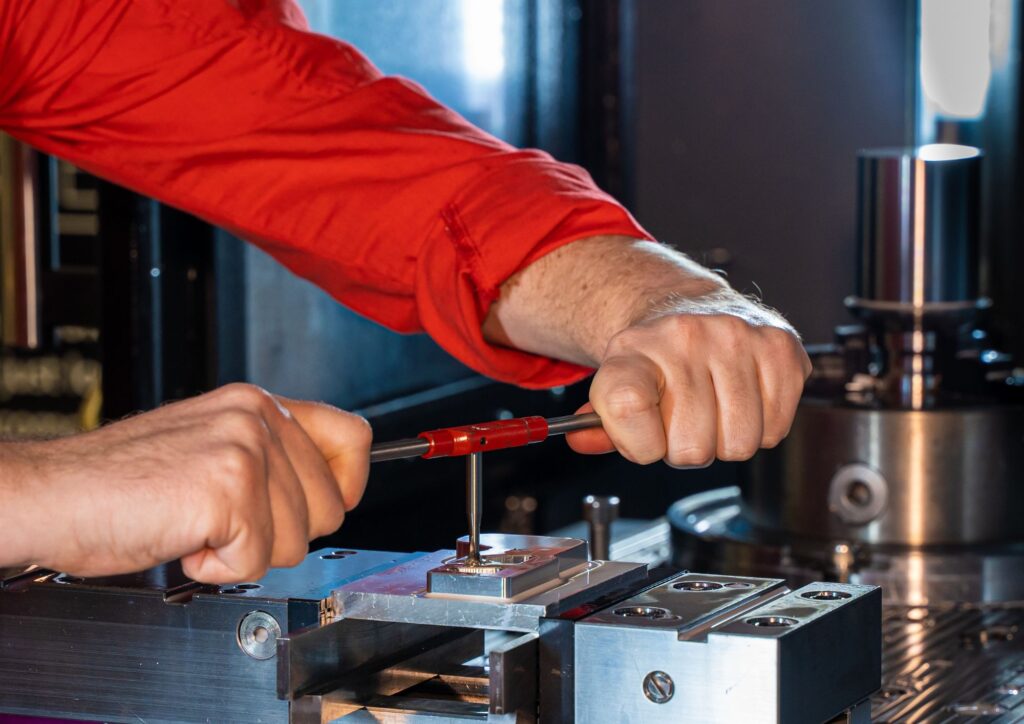
History of EDM
The Electroerosion It was discovered accidentally in 1943 by Soviet scientists BR and NI Lazarenko. While researching methods to protect electrical contacts from erosion, they discovered that controlled electrical discharges could be used to cut and shape metallic materials with great precision. This discovery gave rise to a new machining technique that would revolutionise the manufacture of complex components.
Technological Evolution of Electroerosion
Since its discovery, the Electroerosion has experienced significant technological advances. In the early days, EDM machines were rudimentary and limited in terms of precision and control capacity. However, over time, the development of computer numerical control (CNC) systems allowed for millimetric precision and greater efficiency in the process.
In the 1970s, the introduction of the Wire EDM further expanded the capabilities of this technique. This method uses a conductive wire that moves continuously through the material, allowing for complex and detailed cuts that would not be possible with other machining methods.
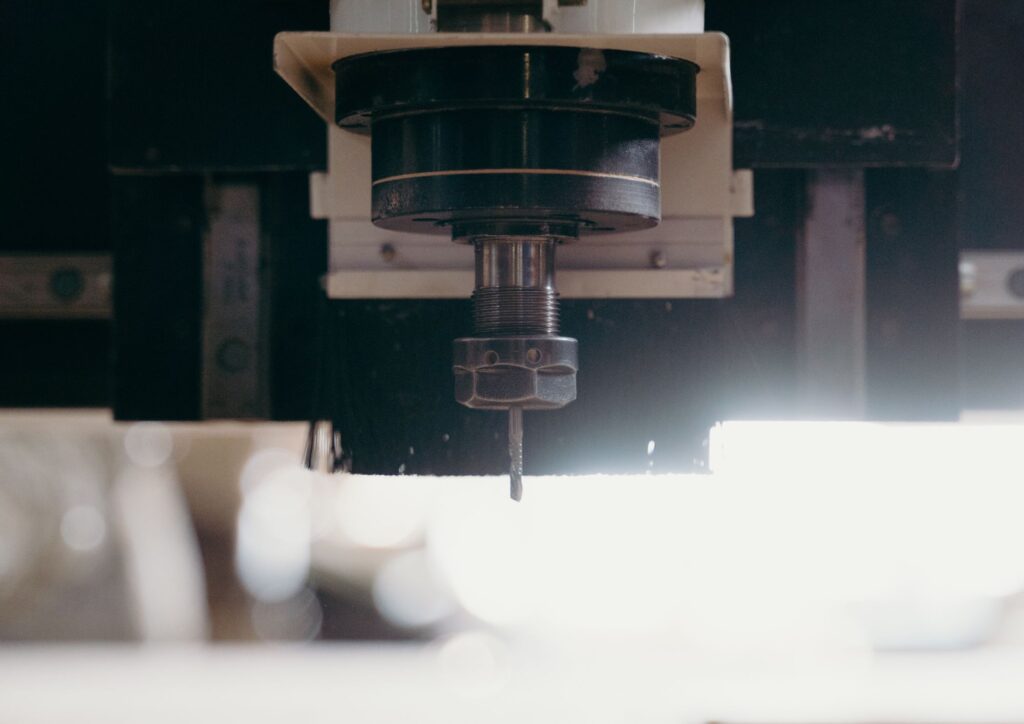
Uses of Electroerosion
The Electroerosion It has become an essential tool in various industries thanks to its ability to work with hard materials and produce parts with high precision. Below are some of its most notable uses.
Automotive Industry
In the automotive industry, the Electroerosion It is used to manufacture critical components such as moulds, dies and engine parts. The precision of this technique allows parts to be created with very tight tolerances, improving vehicle performance and reliability.
Aerospace industry
The Electroerosion It is essential in the manufacture of aerospace components, where precision and the ability to work with advanced materials such as titanium alloys and superalloys are essential. This technique enables the production of complex, high-strength parts that are crucial to aircraft safety and performance.
Medical Industry
In the medical industry, the Electroerosion is used to produce surgical instruments and medical device components. The ability of this technique to create parts with smooth and precise finishes is vital to ensuring the safety and effectiveness of these products. In addition, the Electroerosion It allows working with biocompatible materials, which are essential for medical implants.
The precision and detail offered by the Electroerosion They are ideal for the manufacture of moulds and dies used in the production of plastic and metal parts. This technique allows the creation of moulds with intricate details and smooth surfaces, improving the quality of the final products.
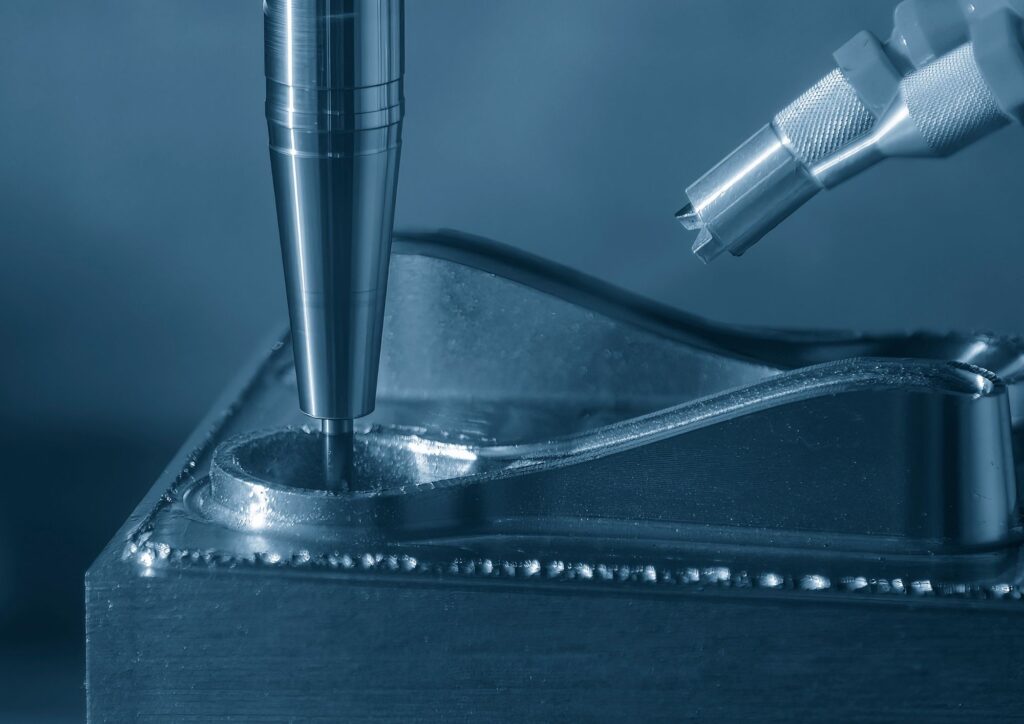
Advantages of Electroerosion
The Electroerosion It offers several advantages that make it preferable over other machining techniques:
- High Precision: Allows extremely precise cuts, which is essential for the manufacture of complex components.
- Working with Hard Materials: It can work with difficult-to-cut materials such as hardened steels and titanium alloys.
- Reducing Tool Wear: Since there is no direct contact between the electrode and the workpiece, tool wear is reduced, prolonging their useful life.
- Versatility: It is applicable in various industries, from automotive to medical, thanks to its ability to create parts with various shapes and sizes.
In short, the Electroerosion is a revolutionary machining technique that has transformed the manufacturing industry. Its development history and multiple applications demonstrate its importance and effectiveness in creating precise, high-quality components. With continuous technological advancements, the Electroerosion will continue to be a key tool in the world of machining.