Learn about the types of molds used in plastics manufacturing and how electroerosion improves precision in their production
The molds of injection of plastic Molds are essential in the production of a wide range of products that we use every day. This process allows the efficient manufacture of parts with complex shapes and precise details. Molds are the basis for producing high-quality items and, depending on their design and use, there are various types that are chosen according to the specific needs of the product. In this article we explain the different types of molds, their applications and how technologies such as electroerosion improve their precision.
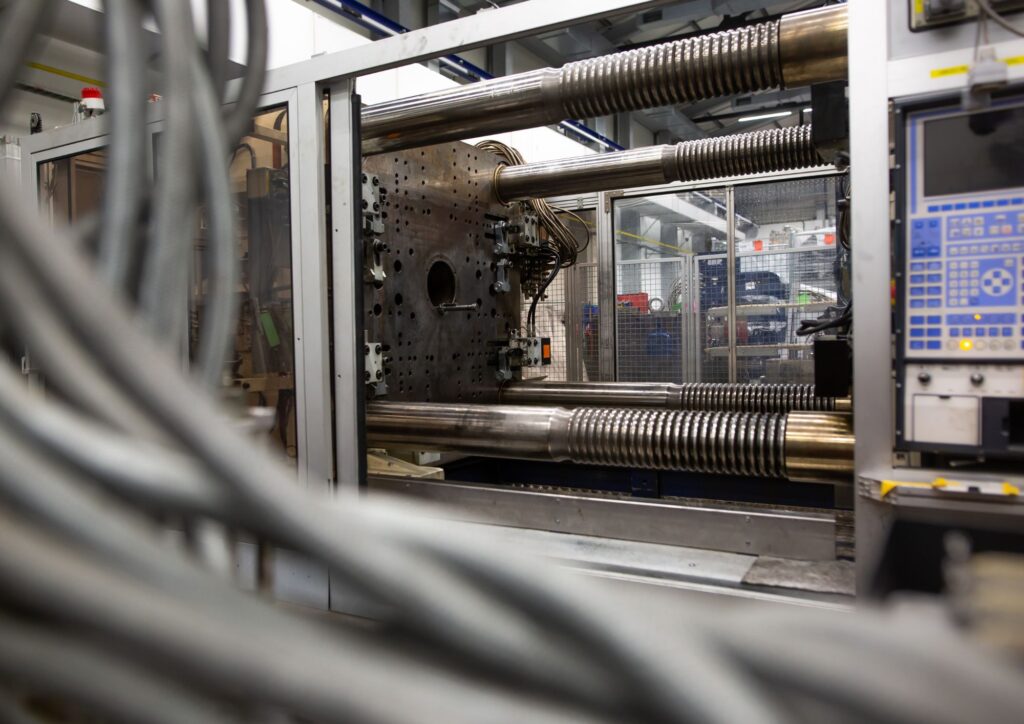
What are plastic injection molds?
The plastic injection process involves melting plastic and then injecting it under pressure into a mold to shape it. The mold, in this context, is the element that determines the final shape of the part, making it a crucial part of the process. Molds allow for the creation of parts with fine details that would be difficult to obtain using other methods. Temperature control, mold material, and design are key factors that affect the quality of the parts produced.
Types of plastic injection molds
There are different types of moulds used in plastic injection, each with specific characteristics that make it suitable for certain products and processes. Below we describe some of the most common ones.
Single cavity molds
Single-cavity molds are those that have a single cavity into which the plastic is injected. They are ideal for producing a single piece in each cycle, which can be efficient when high production volumes are not required. They are common in applications that do not require high complexity, such as covers or small general-use parts. This type of mold is often used to manufacture electronic device housings or small components for household use, for example.
Multi-cavity molds
Multi-cavity moulds are those that have several cavities into which the plastic is injected simultaneously. This type of mould is especially useful when large volumes of identical parts need to be produced at once, which reduces production costs and increases efficiency.
Hot-melt injection molds
Hot-melt moulds have the particularity of keeping the plastic in a molten state throughout the injection process. This allows for obtaining higher quality parts, with a better surface finish and greater precision. They are ideal for producing parts that require high structural integrity.
Cold mold injection molds
In cold injection molds, the plastic is injected at lower temperatures. This type of mold is suitable for less complex or smaller volume parts. In addition, they are easier to handle and repair than hot-cast molds.

How does EDM improve plastic injection mold manufacturing?
The EDM is an advanced technology which allows molds to be made with extreme precision. In this process, a controlled electrical discharge is used to erode material from an electrode and transfer that shape to the mold. EDM is especially useful for creating fine details and intricate cavities that would be difficult to achieve using other methods.
Electrical discharge machining allows working with hard materials such as hardened steel, making it ideal for the manufacture of moulds that require high wear resistance. It also allows creating complex details in moulds with a precision that improves the quality of the injected parts.
Applications of plastic injection molds in different industries
The molds of injection of plastic They have a wide variety of applications in different sectors. From automotive to consumer products manufacturing, every industry takes advantage of the capabilities of molds to obtain high-quality products with the necessary efficiency. Here are some examples:
Automotive industry
In the automotive industry, injection molds are used to manufacture essential parts such as body panels, engine components, and interior trim. The precision and strength of these parts is crucial to ensuring vehicle safety and performance.
Consumer and packaging industry
Injection molds are also key in the production of plastic packaging, such as bottles, caps and other consumer productsThese molds allow efficient production in large volumes, reducing costs and manufacturing times.
Electronics industry
Injection moulds are essential for producing electronic components such as device housings and connectors. Precision in the manufacture of these moulds is crucial, as the parts need to fit perfectly into electronic circuits and devices.
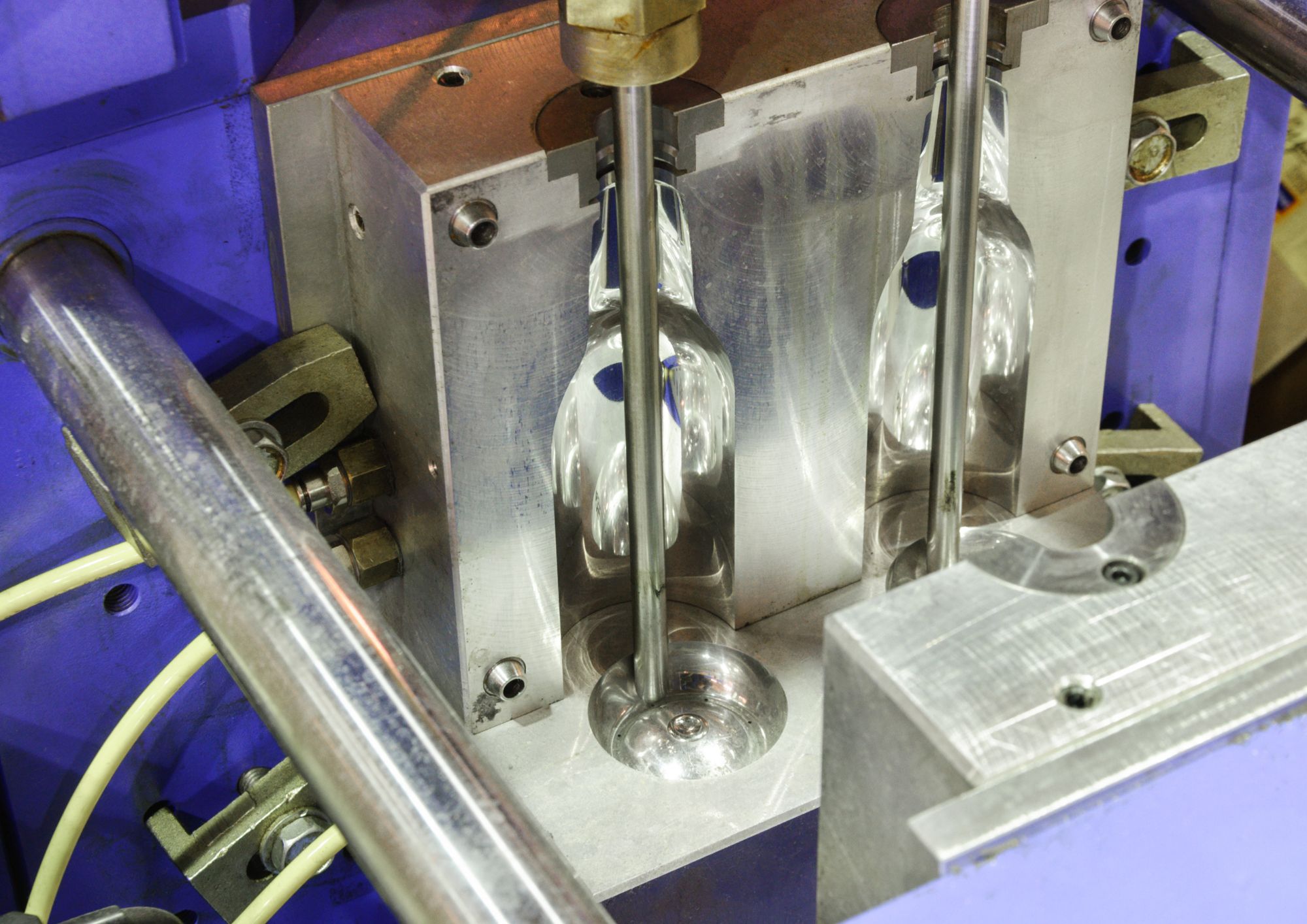
The plastic injection process is essential in various industries, and choosing the type of mold of injection of plastic The right tool can make all the difference in terms of quality, efficiency and costs. EDM has greatly improved the accuracy of mould manufacturing, allowing for more complex and detailed parts to be produced.