This technique allows the manufacture of parts with complex geometries, high precision requirements and difficult materials.
He electrical discharge machining (EDM) is an advanced process used primarily in the manufacturing of parts with complex shapes that require high precision. This technique is based on the erosion of material through repetitive electrical discharges between an electrode and the workpiece. This makes it an ideal tool for parts with intricate geometries, difficult to access or high hardness materials. One of the main advantages of this process is its ability to work with materials that cannot be easily machined using conventional techniques. In addition, the ability to create minute and complex details, with extremely high tolerance, is a prominent feature in the precision industry.
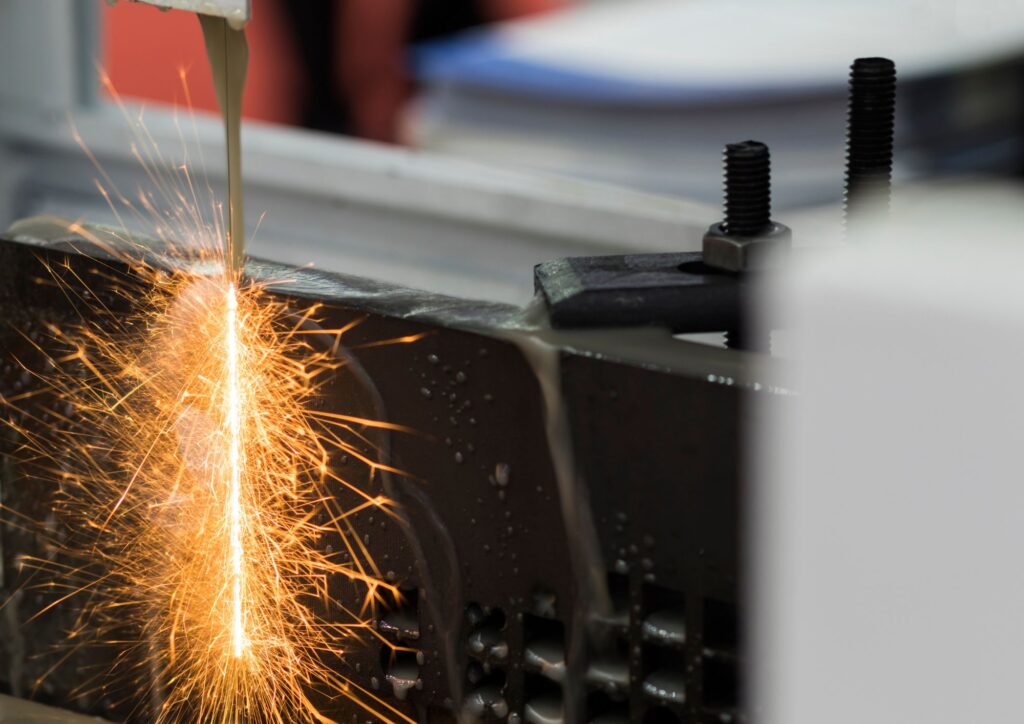
What is electrical discharge machining?
He electrical discharge machining is a manufacturing process based on the removal of material from a workpiece by means of erosion caused by electrical impulses between a conductive electrode and the workpiece material. This process is mainly used when it is necessary to machine complex shapes or make precise cuts in hard materials.
TO difference from conventional machining, which is based on friction and pressure, EDM uses the electrical properties of materials. The electrode moves in a controlled manner relative to the workpiece, generating a series of sparks that remove material from the piece. This process is ideal for parts with complex geometries that cannot be manufactured using other methods such as turning or milling.
The importance of precision in machining complex parts
He electrical discharge machining It is a highly valued technique in the precision industry due to its ability to produce parts with extreme accuracy. This is especially valuable in sectors such as automotive and aerospace, where tight tolerances and intricate geometries are critical.
For example, in the manufacture of moulds for precision components or in the creation of micro components, the EDM's ability to work with precision at the micron level is a decisive factor. The technique allows the creation of complex cavities, very small perforations and fine details without compromising the integrity of the material.
In addition, electroerosion machining offers great flexibility in the manufacture of parts with geometric shapes that are difficult to achieve using other traditional machining processes.
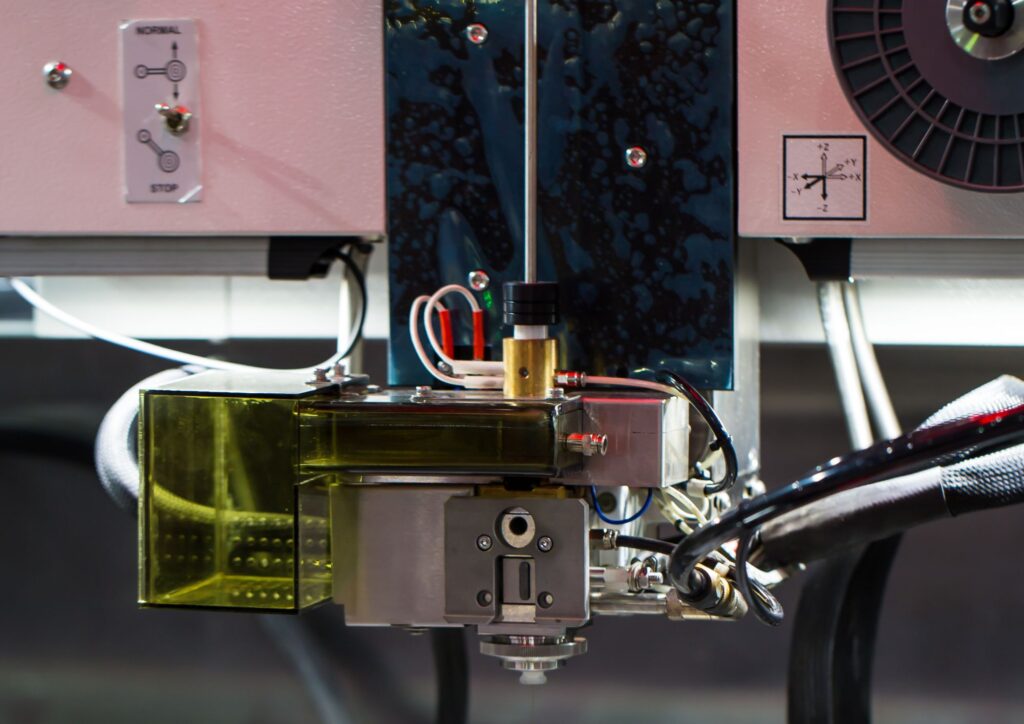
Why is EDM ideal for parts with complex geometries?
One of the main reasons why the electrical discharge machining What is so valuable in manufacturing complex parts is its ability to work with complicated geometries that other machining processes cannot achieve. EDM is capable of creating highly detailed shapes, even those that include deep cavities, very fine holes, or details that would require special cutting tools in other methods.
The process is especially useful for parts that have hard-to-reach spaces or high-precision features, such as electronic components or plastic injection molding parts. EDM allows for extremely fine cutting and drilling without deforming the surrounding material. It also allows for machining titanium without thermal deformation, achieving more precise cuts and superior finishes.
Machining of deep cavities and shapes
One of the outstanding capabilities of EDM is its ability to create deep cavities and complex shapes that other methods cannot achieve. Through controlled erosion, the electrode can penetrate the material to great depths without affecting the rest of the part, which is especially useful in mold and die manufacturing.
This process enables the creation of cavities with millimetre precision, which is essential in applications such as the production of moulds for automotive components or electronic products.
Ability to work with hard materials
Another advantage of electroerosion is its ability to work with high hardness materials difficult to machine. Since the process does not rely on physical contact between the electrode and the workpiece, it can cut materials that would be problematic for other machining processes, such as turning or milling. This benefit is particularly relevant in the manufacture of components for the aerospace, automotive and energy industries, where durability and strength of materials are essential.
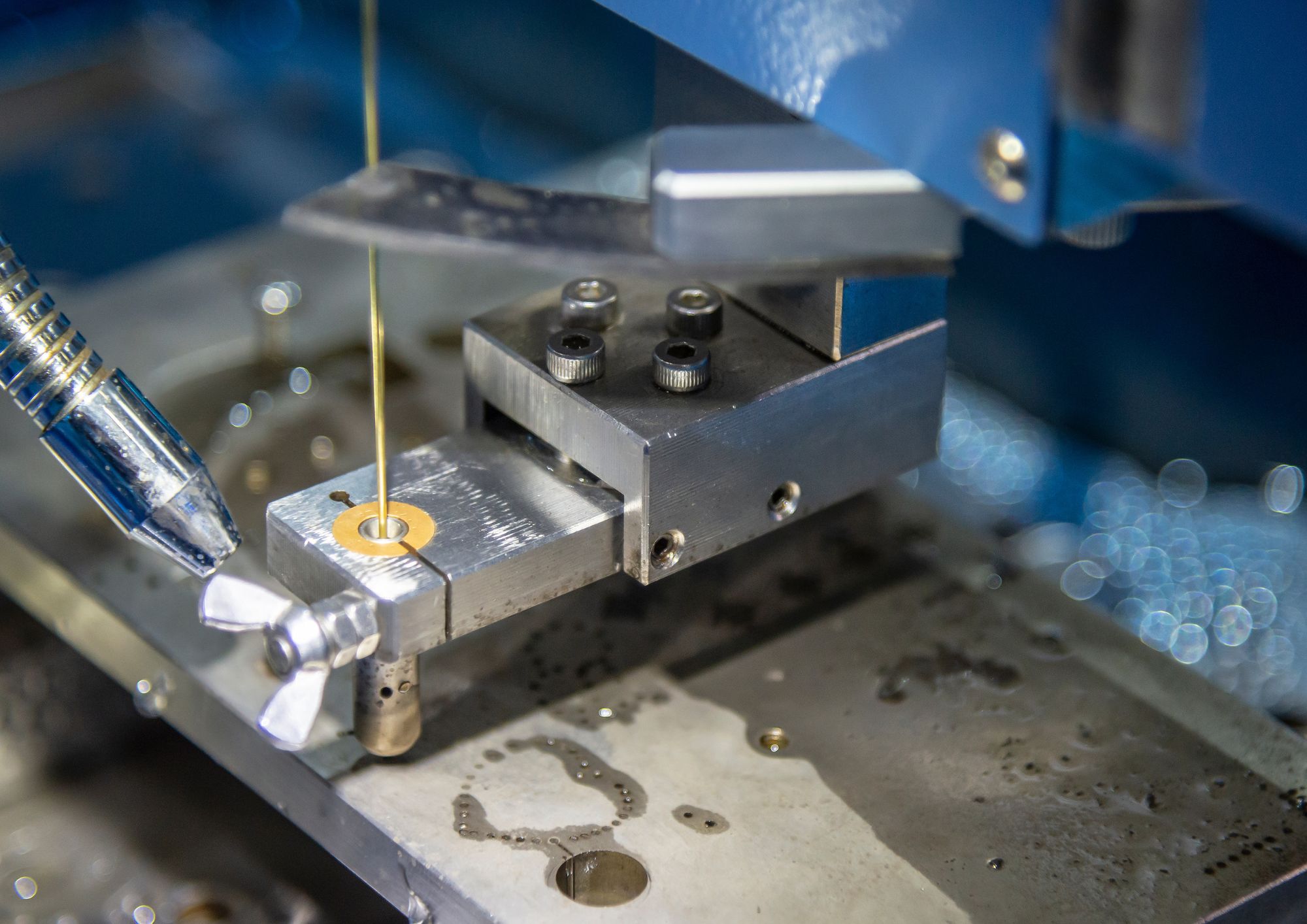
He electrical discharge machining EDM is one of the most advanced and precise technologies available for manufacturing complex parts. Its ability to work with hard materials and create intricate geometries makes this technique an ideal choice for sectors such as automotive, aeronautics and mold making. If your company needs to manufacture parts with micron-level precision, EDM is a must-have option that can deliver results that other methods are unable to achieve.