A machining process for geometrically complex parts
The automotive sector is one of the most demanding in terms of precision, durability and efficiency in the manufacture of components. The constant evolution of designs and market demands require advanced technologies that allow achieving higher quality standards. In this context, the wire EDM (Wire EDM) has established itself as an essential tool in the automotive sector, thanks to its ability to work with high precision and in extremely hard materials, transforming the Production of complex parts in the automotive industry.
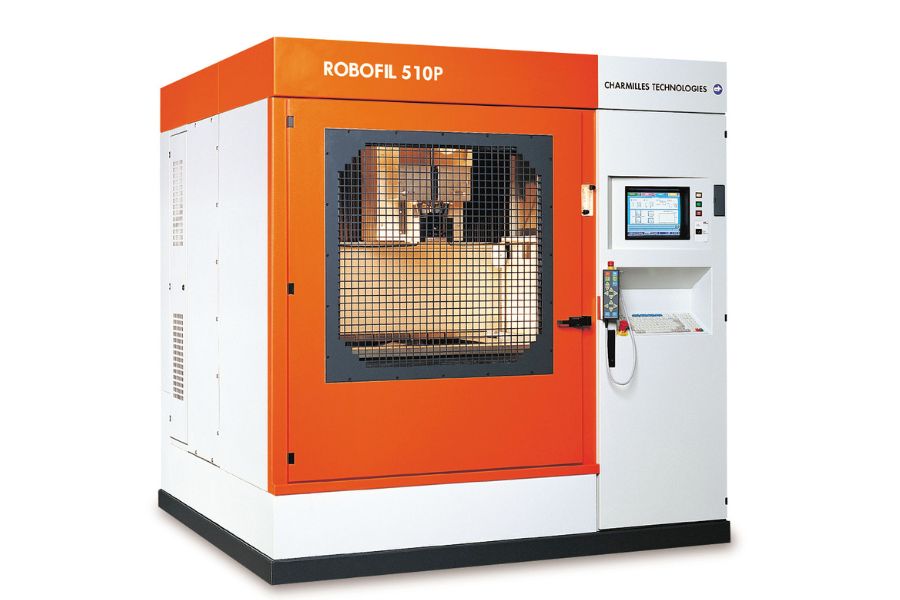
Manufacturing of shades, molds and components
The wire EDM It is a non-conventional machining process that allows the creation of parts with extremely complex geometries and fine details, impossible to achieve with traditional methods. In the automotive sector, this technique is mainly applied in the Manufacturing of precision dies, moulds and components requiring tight tolerances and flawless surface finishes.
1. Manufacturing of dies and matrices
Dies and molds are essential for the stamping of car bodies and the shaping of metal components. wire EDM allows these tools to be manufactured with millimetre precision, ensuring that the final parts meet exact specifications.
- Advantages:
- High precision in edges and details
- Ability to work with hardened steels without affecting their mechanical properties
- Production of complex geometries required for custom molds
2. Production of gears and transmission components
Gears and transmission parts are critical to the operation of vehicles. These components require high wear resistance and a perfect fit. wire EDM It facilitates the manufacturing of these parts in high hardness materials, such as alloy steels and tungsten carbide.
- Featured Applications:
- Precision gears for gearboxes
- Axles and assembly parts
3. Prototypes and production of unique pieces with wire EDM
In the development phase of new models, manufacturers need high-quality prototypes for testing and validation. wire EDM It is ideal for producing prototypes of metal components with great speed and precision, reducing development time.
- Examples:
- Prototypes of fuel injection systems
- Specific components for aerodynamic testing
4. Suspension elements and safety systems
Suspension systems and vehicle safety structures, such as airbags and seat belts, also benefit from the wire EDM. This technique ensures that the metal components involved meet strict quality and durability standards.
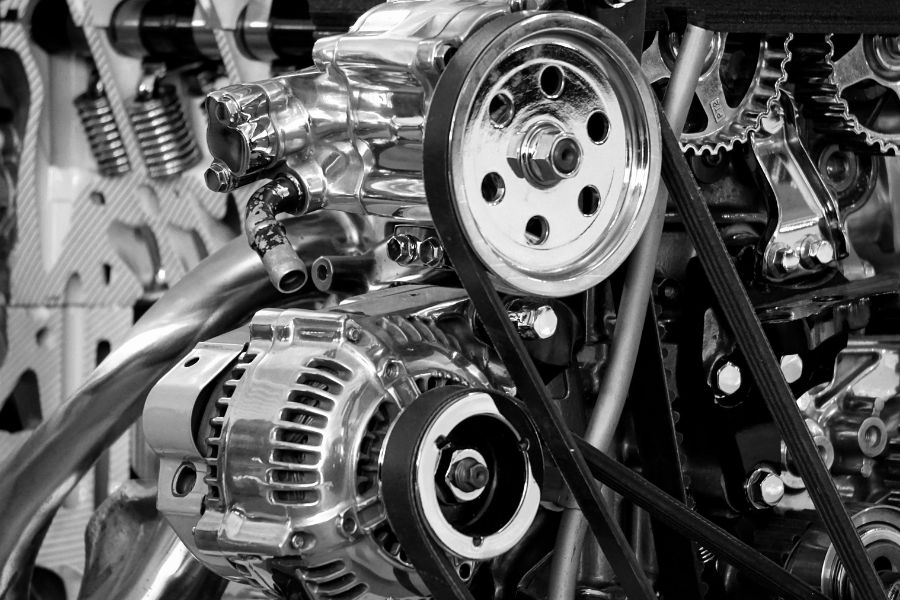
Benefits of wire EDM in the automotive industry
1. High precision and repeatability
The wire EDM allows working with tolerances of up to micrometers, which guarantees the accuracy of parts. Furthermore, this precision is replicable, ensuring consistency in the series production.
2. Ability to work with hard materials
The automotive industry is increasingly using advanced materials, such as titanium alloys and hardened steels, to improve vehicle performance and durability. wire EDM can cut these materials without compromising their structural integrity.
3. Flexibility in design
This technique allows the creation of complex shapes and geometries that would be impossible to achieve with conventional machining methods. This is especially valuable in the custom component design and molds for high-end vehicles.
4. High quality finishes
The process of wire EDM produces parts with smooth, burr-free surfaces, reducing or eliminating the need for secondary finishing processes. This saves time and costs in manufacturing.
5. Sustainability and efficiency
To the do not generate significant chips or waste, becomes a cleaner process than other machining techniques. In addition, it allows for efficient use of the material, reducing waste.
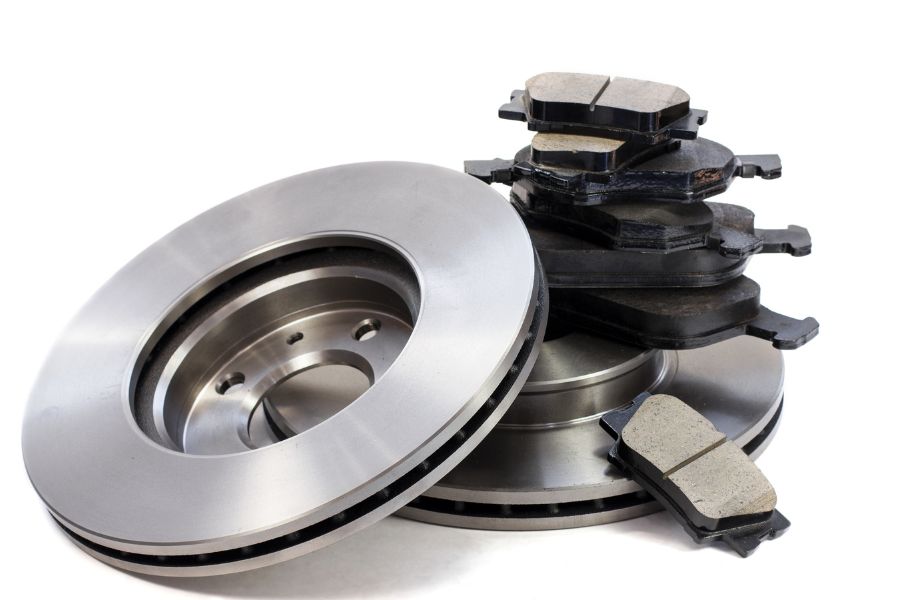
Challenges and future of wire EDM in the automotive industry
The future of wire EDM in the automotive industry looks promising, especially with the growing Demand for electric and autonomous vehicles. These new models require smaller, more precise components and advanced materials, where the wire EDM has a crucial role.