Advanced techniques for shaping metals and alloys
He electrical discharge machining It is based on the phenomenon of electrical erosion. It consists of generating a series of controlled electrical discharges between an electrode and the work piece, both immersed in a dielectric fluid. These discharges generate intense localized heat that melts and vaporizes small portions of the material.
EDM is divided into two main categories:
- Sinker EDM: It uses a specifically shaped electrode that is pressed against the workpiece.
- Wire EDM: It uses a thin conductive wire that cuts the material following a programmed pattern.
Both methods are highly effective for producing high-precision parts, but each has specific applications depending on the project requirements.
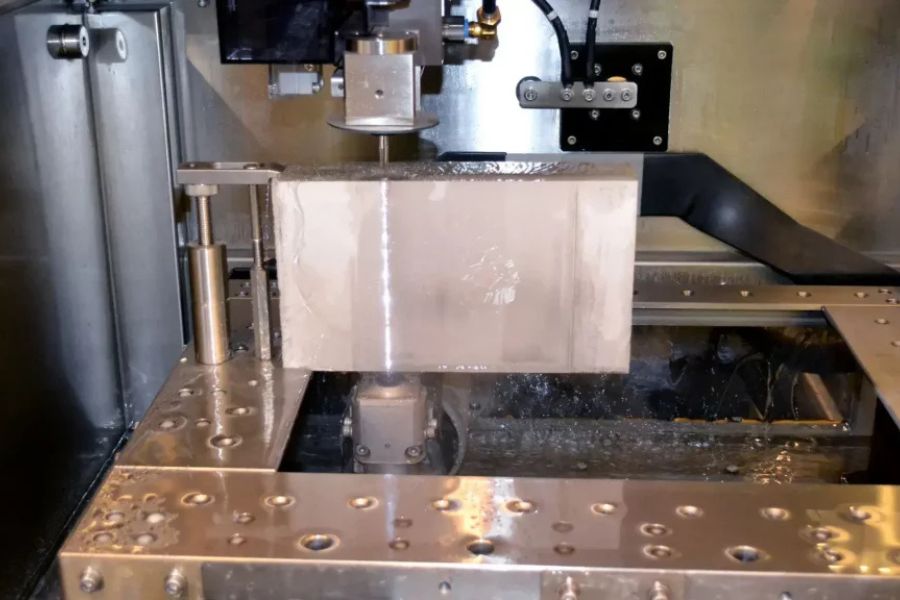
Advantages of EDM machining
- Extreme precision: Ideal for manufacturing components with very tight tolerances, up to micrometers.
- Ability to work difficult materials: Such as super resistant alloys, tungsten carbide or titanium.
- Manufacturing complex geometries: Allows the creation of intricate shapes that would be unfeasible with traditional tools.
- Absence of mechanical stress: No direct physical force is applied, which prevents deformation or damage to the part.
These features make the electrical discharge machining is an irreplaceable technique in sectors such as aeronautics, automotive, the medical industry and mold manufacturing.
CAD/CAM assisted EDM
Using advanced CAD/CAM software allows machining to be designed and simulated before it is executed. This digital integration improves accuracy, optimizes production times and reduces human error. In addition, CAD/CAM systems can calculate complex electrode or wire paths, maximizing process efficiency.
EDM in micro manufacturing
In the era of miniaturization, EDM has been adapted to manufacture tiny, high-precision parts such as electronic components, microturbines or surgical tools. In this field, ultra-thin electrodes and fine-tuned parameters are used to achieve perfect finishes in minuscule dimensions.
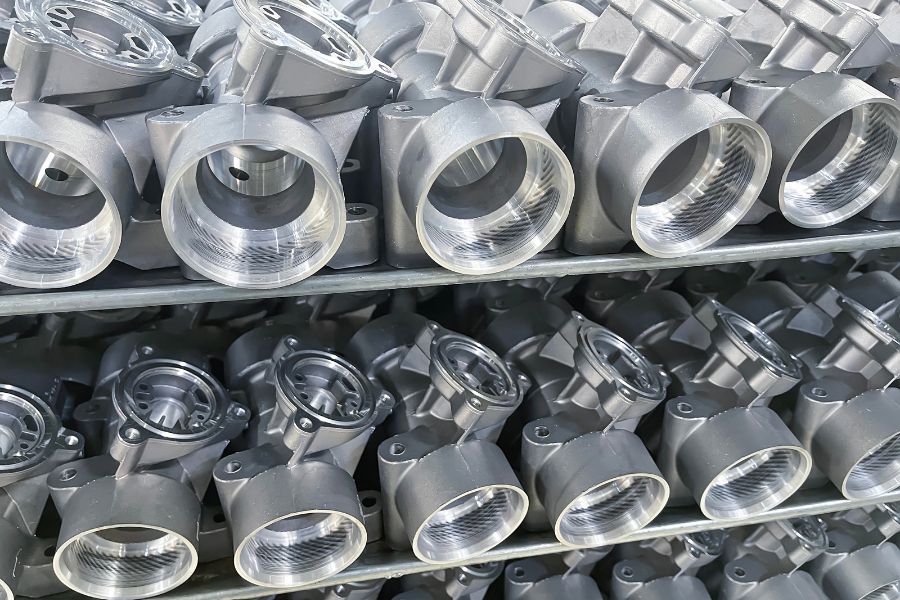
Industrial applications of advanced EDM
Manufacturing of moulds and dies
He EDM It is essential in the production of moulds and dies for plastics and metals, as it allows the creation of complex cavities with an exceptional surface finish. Advanced techniques, such as high-speed EDM and the use of multiple axes, have significantly reduced production times.
Aerospace industry
In this sector, EDM is used to manufacture aircraft engine components such as turbine blades and parts made of super-strong materials. The ability to work with tight tolerances and exotic materials makes it a crucial technology for meeting quality and safety standards.
Medicine and surgical devices
The manufacturing of medical instruments, such as surgical scissors, needles and prosthetic molds, greatly benefits from EDM. The ability to produce parts with micrometer precision is critical in this industry.
Automotive
In the automotive industry, EDM enables the creation of components such as fuel injectors, gears, and stamping dies with high precision and consistency. It also facilitates the development of complex prototypes during the design of new vehicles.
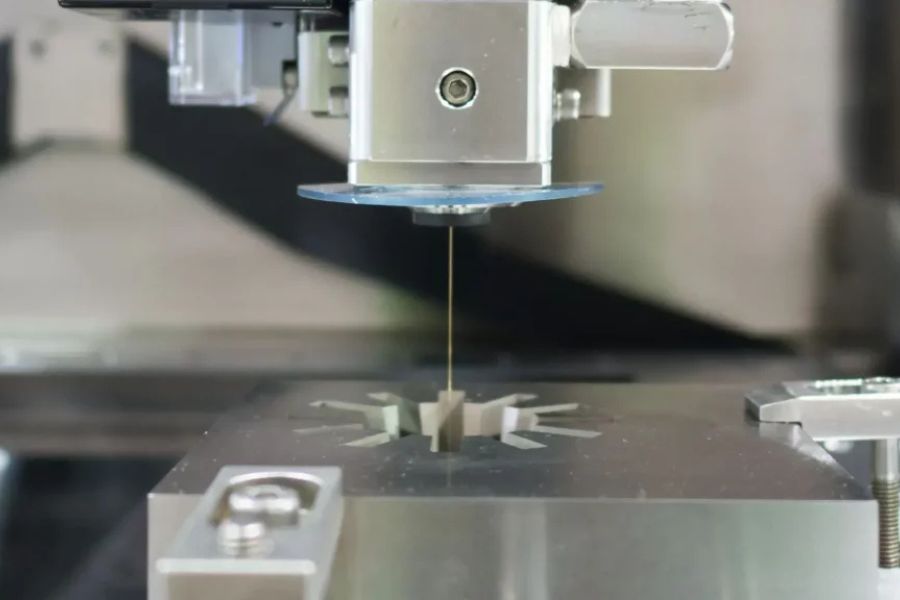
Sustainability and the future of EDM machining
He electrical discharge machining EDM is moving toward more sustainable methods, such as the reuse of dielectric fluids and the use of energy-efficient technologies. As demands for precision and efficiency increase in manufacturing, EDM will continue to evolve to meet the needs of modern industry. The development of advanced electrode materials and smarter control systems promise to revolutionize this technology even further.
He electrical discharge machining EDM is an indispensable tool in the manufacturing of complex, high-precision parts. Advanced techniques such as the use of CAD/CAM, improved dielectric fluids, and multi-axis machines have expanded the possibilities of EDM in a variety of industries. With its ability to work with difficult materials and intricate shapes, this technology will continue to be a key pillar in advanced manufacturing in the future.
Advantages of EDM machining
EDM machining has become a preferred solution in many industries thanks to its numerous advantages:
1. High precision and surface finish
The ability to control the size and intensity of electrical discharges allows for extremely tight tolerances and high quality surface finishes, eliminating the need for additional processes such as polishing.
2. Machining of hard materials
Unlike traditional methods, EDM does not depend on the hardness of the material. This makes it ideal for working with high-strength alloys that would be difficult to machine by milling or turning.
3. Without shear forces
Since there is no physical contact between the electrode and the work, mechanical forces are eliminated, reducing the risk of deformations in delicate or thin parts.
4. Complex geometries
EDM makes it possible to create intricate shapes, deep cavities and angles that are impossible to achieve with conventional tools.
He electrical discharge machining EDM is an indispensable technology in precision manufacturing, offering solutions that other methods cannot match. Although it has challenges, its advantages in terms of precision, versatility and ability to work with hard materials make it an essential tool in multiple sectors. As technology continues to advance, EDM will continue to play a crucial role in industrial innovation.