How wire EDM is revolutionising the manufacturing of key tools for the food industry, ensuring precision and regulatory compliance
The food industry demands tools and components that are not only accurate, but also safe and durable. This is where the wire EDM plays a crucial role, offering advanced technological solutions for the manufacturing of moulds, blades and other essential elements in food production processes.
This article looks at how this innovative method works, its specific applications in the food industry, and the advantages it offers over other traditional machining techniques. We will also explore how to choose the right supplier to ensure the best results.
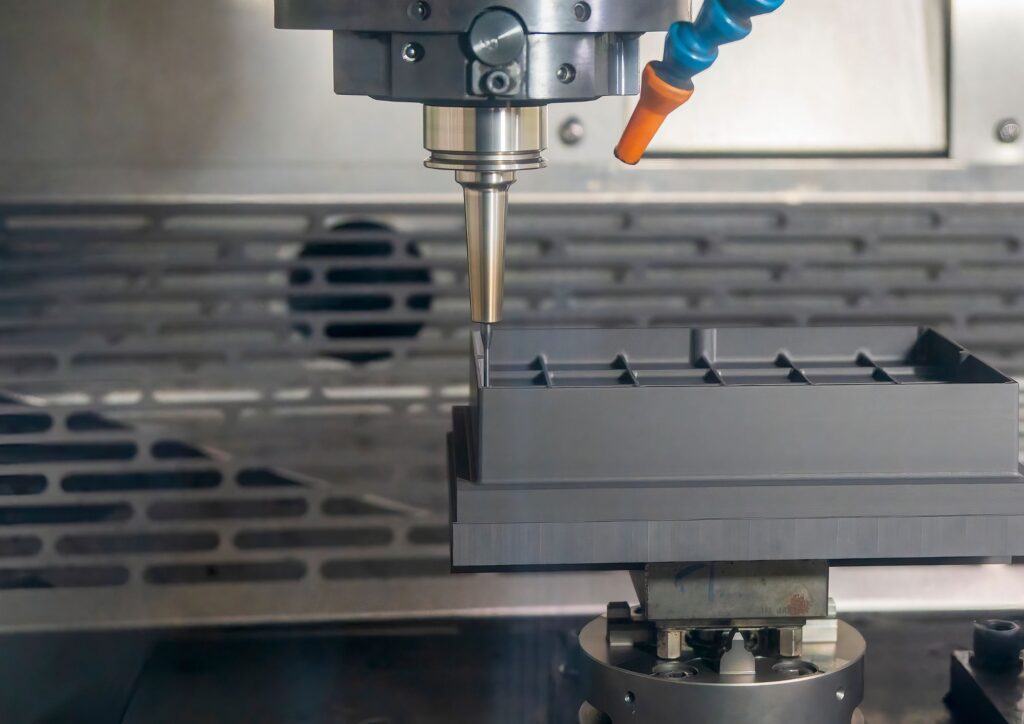
What is wire EDM and why is it relevant in the food industry?
The wire EDM It is an unconventional machining process that uses a conductive wire and controlled electrical discharges to cut conductive materials with extreme precision. This method does not exert mechanical force on the workpiece, making it an ideal solution for working on delicate components or those with complex geometries.
In the food sector, the requirements are even more demanding:
- Millimeter precision to meet specific mold and tool designs.
- Compatibility with safe materials for food, such as corrosion-resistant stainless steels.
- Regulatory compliance, guaranteeing hygiene and safety in each manufactured component.
Thanks to these benefits, wire EDM is key to optimizing processes and ensuring that food tools meet the highest quality standards.
Applications of wire EDM in the food industry
Wire EDM allows the creation of highly precise and complex mould designs, essential for producing plastic, aluminium and other material containers. Here are some of its advantages:
- Extreme precision in design: Ideal for packaging that requires detailed shapes or specific patterns.
- Hygiene guaranteed: Smooth, blemish-free surfaces facilitate cleaning and prevent residue build-up, ensuring regulatory compliance.
In addition, in food production lines, tools such as cutters, blades and dies must be highly precise to ensure accurate and consistent cuts.
- Cutters and blades: Made of wear and corrosion resistant materials, they offer long service life and maintain processing quality.
- Custom matrices: They allow machines to be adapted to the specific needs of each product, from bread to meat products.
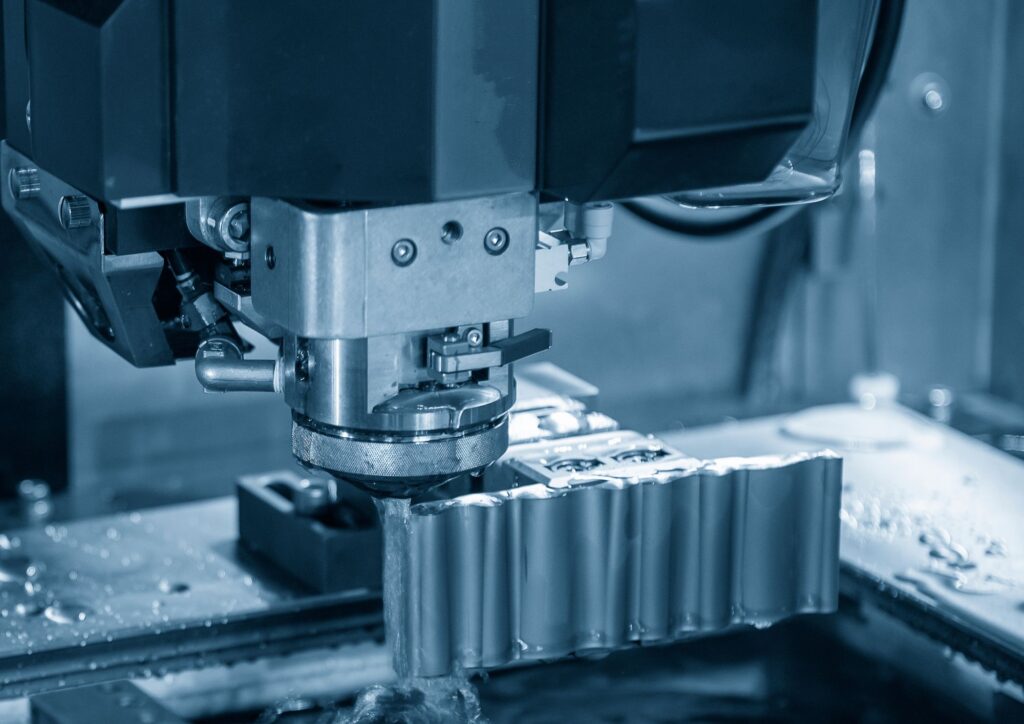
Advantages of wire EDM over other methods in the food sector
The wire EDM offers multiple benefits compared to other cutting methods:
High precision without thermal deformation
By not generating excess heat, it prevents deformations in sensitive materials, such as stainless steels used in the food industry.
Compatibility with food safe materials
It allows you to work with materials that comply with food regulations, such as stainless steel and corrosion-resistant alloys.
Reduction of costs and errors
By minimizing the need for rework or subsequent adjustments, manufacturing costs are optimized and consistent quality is ensured.
Tips for choosing an EDM service provider in the food industry
Choosing the right supplier is key to achieving high-quality results. Some aspects to consider include:
- Experience in the food sector: Working with companies that understand the specific regulations and requirements of the sector ensures better results.
- Certifications and advanced technology: A supplier that uses modern machinery and has quality certifications (such as ISO) is essential to meet industry standards.
- Customization capability: Make sure the supplier can accommodate the particular needs of your project, whether in terms of design or materials.
Reviewing success stories and asking for references are additional steps that can help you make an informed decision.
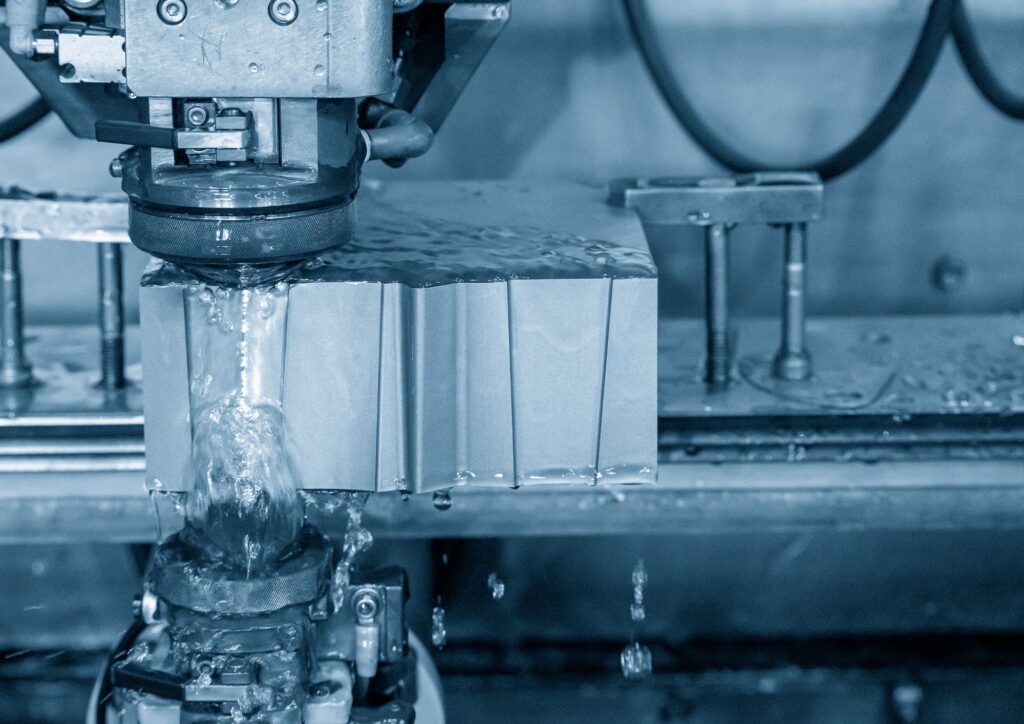
The wire EDM It is an essential technology for the food industry, where precision, hygiene and efficiency are essential. From the manufacture of moulds and tools to machine components, this method guarantees high-quality results adapted to the demands of the sector.