We explain the operation, applications, and advantages of wire EDM in industrial manufacturing.
The cut by wire EDM It is a high-precision machining process that uses an electrically charged conductive wire to cut conductive materials using small electrical discharges. This process allows for the manufacture of parts with complex geometries and very tight tolerances, making it an indispensable tool in sectors requiring high-precision machining, such as the automotive, aerospace, and medical industries, among others. We'll tell you much more in this article.
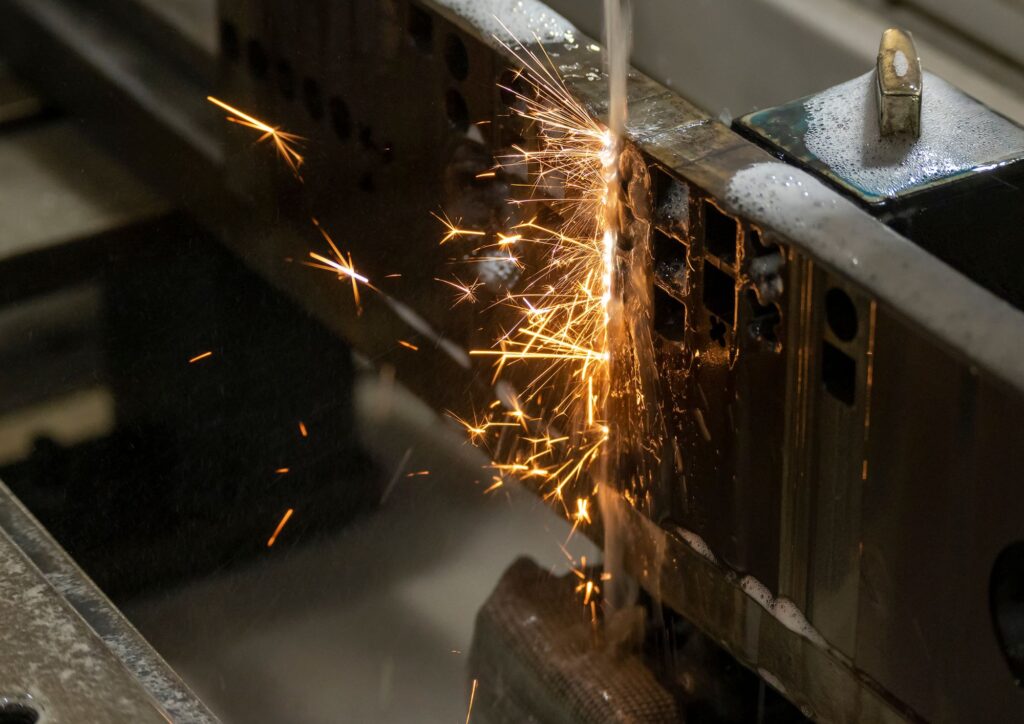
Wire EDM
How does this type of machining work?
The wire EDM It is based on a cutting principle without direct physical contact between the tool and the workpiece. In this process, a conductive wire, usually made of copper or brass, moves through the material to be cut while electrically charged. The electrical discharges that occur between the wire and the material generate extreme heat, which vaporizes small portions of the material, eroding it with high precision.
He wire EDM system It uses a dielectric fluid to cool and remove debris generated during the cutting process, ensuring clean, contaminant-free finishes.
What materials are suitable for wire EDM?
Wire EDM is especially effective on electrically conductive materials. Common materials processed using this technique include metals such as steel, titanium, nickel alloys, hardened steels, and other high-hardness metals. This process is particularly useful for cutting materials that are difficult to machine using conventional methods, such as pre-hardened metals or special alloys.
In addition, the wire EDM cutting It allows working with materials with complex geometries and offers high-precision finishes, which is essential in industries that require very tight tolerances.
Applications in industry: automotive, aerospace, electronics, food, medical devices, etc.
This type of machining is essential in various industrial sectors.
- Automotive industry: is used to make dies and matrices that are used in the production of high-precision parts, such as gears and engine components.
- Aerospace industryWire EDM allows the manufacture of complex parts for engines and aeronautical structures, using materials such as titanium and special alloys.
- Electronic industry: benefits from this process to manufacture precision components, such as connectors and printed circuits.
- Food industry: used to create injection molds for plastic products.
- Medical industry: to produce high-precision parts, such as surgical implants and cutting tools.
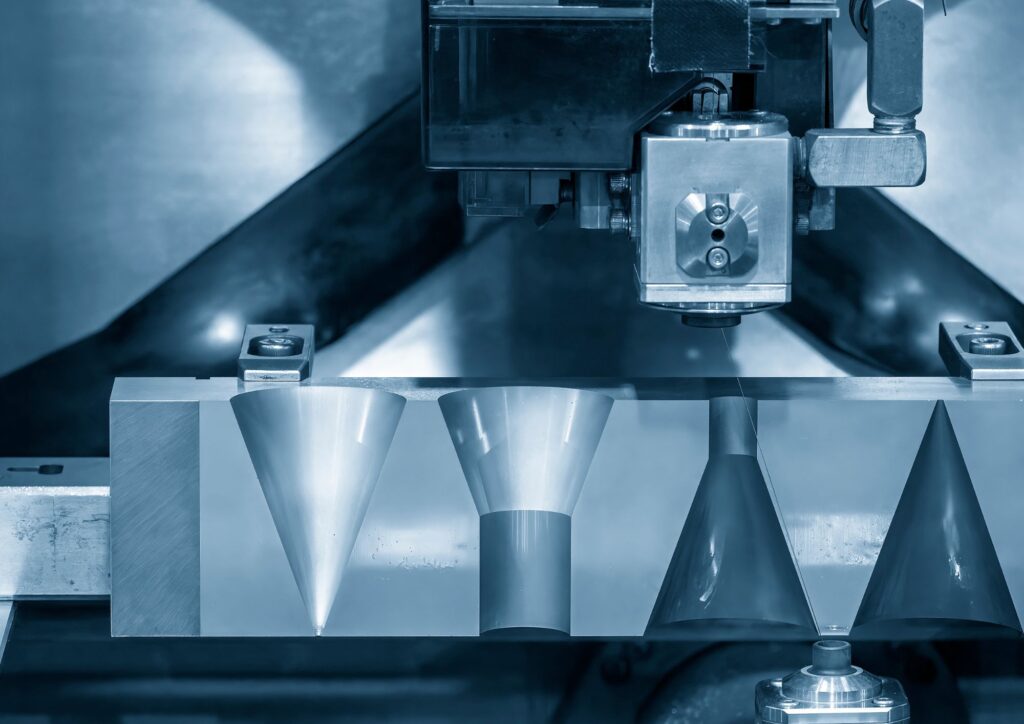
Advantages and disadvantages of wire EDM
The wire EDM It allows the production of parts with extremely complex geometries and very tight tolerances, which is not possible with conventional machining methods. Furthermore, this technique offers high precision without physical contact, minimizing the risk of thermal deformation in the workpiece. Another advantage is that no mechanical forces are generated, which reduces the likelihood of damage to the parts during the process.
However, there are some limitations. First, wire EDM can only be used on conductive materials, which limits its applicability in certain fields. Furthermore, this process is slower compared to traditional machining methods, which can increase production times. It also presents limitations when processing very thick parts.
Wire EDM vs. other techniques
The sinking EDM is another EDM technique, but unlike wire EDM, it uses a solid electrode that penetrates the material. This technique is ideal for creating complex shapes in large, thick parts. Although both techniques use electrical discharges to erode the material, wire EDM is more precise for detailed cuts and thin parts.
The electrical discharge drilling It is used to create tiny, deep holes in conductive materials using electrode tubes. This technique is especially useful for creating complex internal cavities, such as cooling holes in turbines or microperforations in fuel injectors. Although it has some similarities to wire cutting, it is specifically used for drilling, not for contour-cutting.
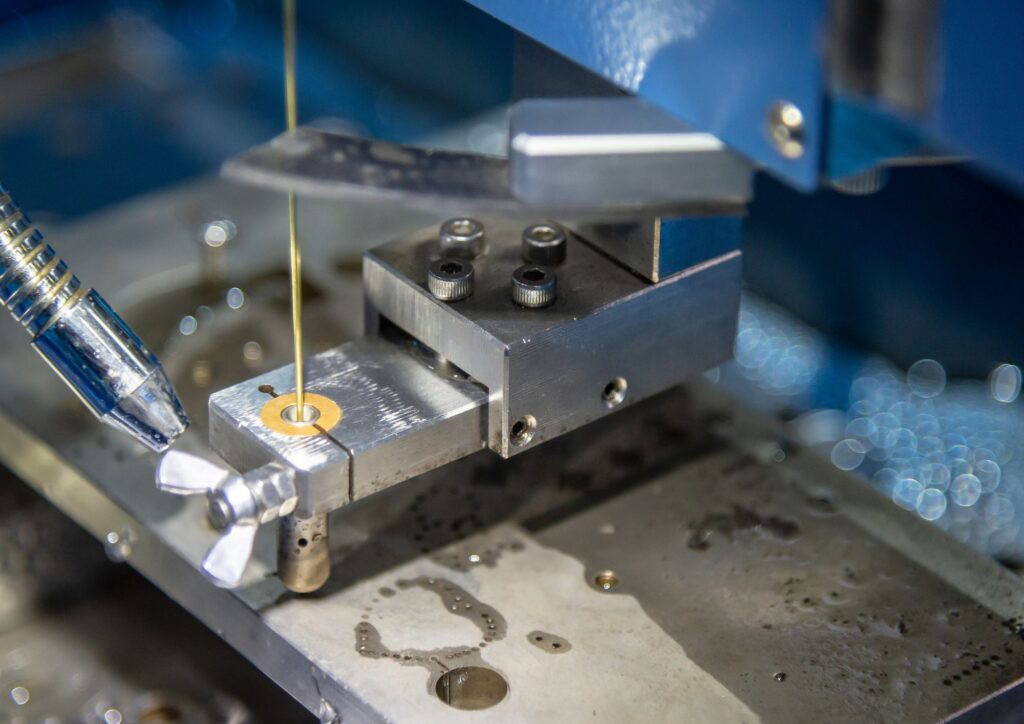
The wire EDM It is a fundamental technique in the manufacturing of high-precision parts with complex geometries. Its ability to work with materials that are difficult to machine using other methods makes it an indispensable tool in sectors such as the automotive, aerospace, electronics, medical, and many others. Although it has some limitations in terms of speed and the types of materials it can process, its advantages in terms of precision, finish, and versatility position it as an ideal option for numerous industrial applications.
When choosing a wire EDM company, such as Electroerosiones Navarra, it's crucial to consider factors such as experience, technology, and success stories in specific industrial sectors to ensure the best results in the manufacture of high-quality parts.