Discover how this cutting method offers precision and efficiency in the manufacturing of complex industrial parts.
He wire EDM cutting It is a widely used method in industries where precision and detail are essential. This process, based on electrical and thermal principles, allows working with a wide range of materials without compromising the final quality of the product.
In sectors such as the automotive, aviation and mould manufacturing industries, this technique has proven to be an efficient solution compared to traditional methods. In this article we will explore in detail how the process works, its main advantages and why it is positioned as one of the best options for precision cutting.
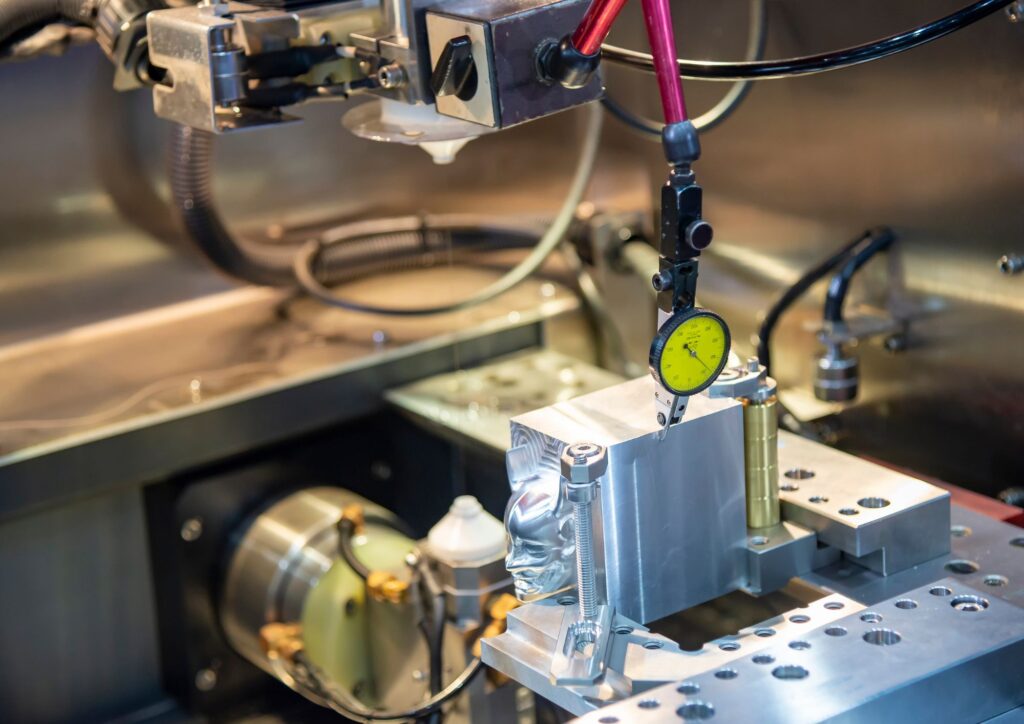
What is wire EDM cutting and how does it work?
He cut by wire EDM It is a technique that uses a conductive wire, usually made of brass or copper, to cut parts using controlled electrical discharges. This method does not exert mechanical force on the material, making it an ideal option for working on delicate parts or those with complex geometries.
The cutting is carried out by immersing the piece in a dielectric bath and generating electrical discharges between the wire and the material. These discharges produce small erosions that, when repeated at high speed, allow for extremely precise cuts.
A wide variety of conductive materials can be worked with, such as hardened steels, titanium, aluminum and other alloys used in high-tech applications.
The machines consist of a discharge generator, a numerical control system (CNC) for precise movements and a conductor wire that moves continuously during the process. The dielectric bath plays a key role in cooling the part and removing residues.
Main advantages of wire EDM cutting
He wire EDM cutting It offers multiple advantages that differentiate it from other precision methods:
Extreme precision in complex parts
Thanks to its ability to make cuts with tolerances of up to microns, this technique is ideal for manufacturing components with very fine details, such as dies, moulds and parts for the aeronautical sector.
Compatibility with a wide range of materials
Unlike other methods, the hardness of the material does not matter: wire cutting can work from soft to the most resistant metals, without causing deformations or defects on the edges.
Less thermal deformation
By not generating intense localized heat, as occurs in laser cutting, the material maintains its original properties, avoiding internal tensions that could compromise its functionality.
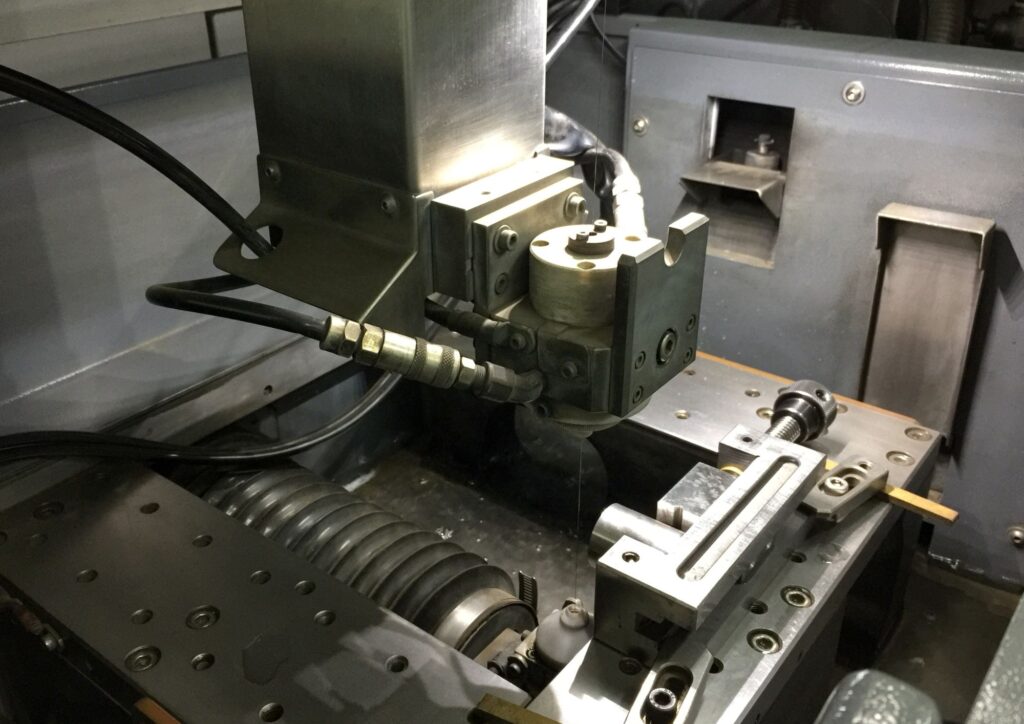
Comparison with other precision cutting methods
He wire EDM cutting stands out from other methods for its precision and versatility. Below is a comparison with two common techniques:
Wire EDM cutting and CNC machining
- CNC machining is fast and efficient for simple shapes, but has limitations on complex geometries and extremely hard materials.
- Electrical discharge machining allows intricate parts to be processed without mechanical wear, although the operating time may be longer.
Differences with laser and waterjet cutting
- Laser cutting is efficient on thin materials, but generates heat that can warp sensitive parts.
- Waterjet is versatile, but it does not achieve the same precision nor is it suitable for very small parts or those with fine details.
Key applications of wire EDM cutting in industry
The flexibility and precision of the wire EDM cutting They make it into a indispensable tool in many sectors:
- Use in stamping moulds and dies: In the manufacture of moulds and dies, this technique ensures impeccable finishes and exact tolerances, essential for processes such as cold stamping.
- High precision components in automotive and aviation: In the automotive and aerospace industries, it is used to manufacture critical parts such as injectors, turbine components and assembly dies.
- Manufacturing of specialized tools: Tools used in sectors such as food, medicine and electronics depend on this technology to achieve the required levels of precision.
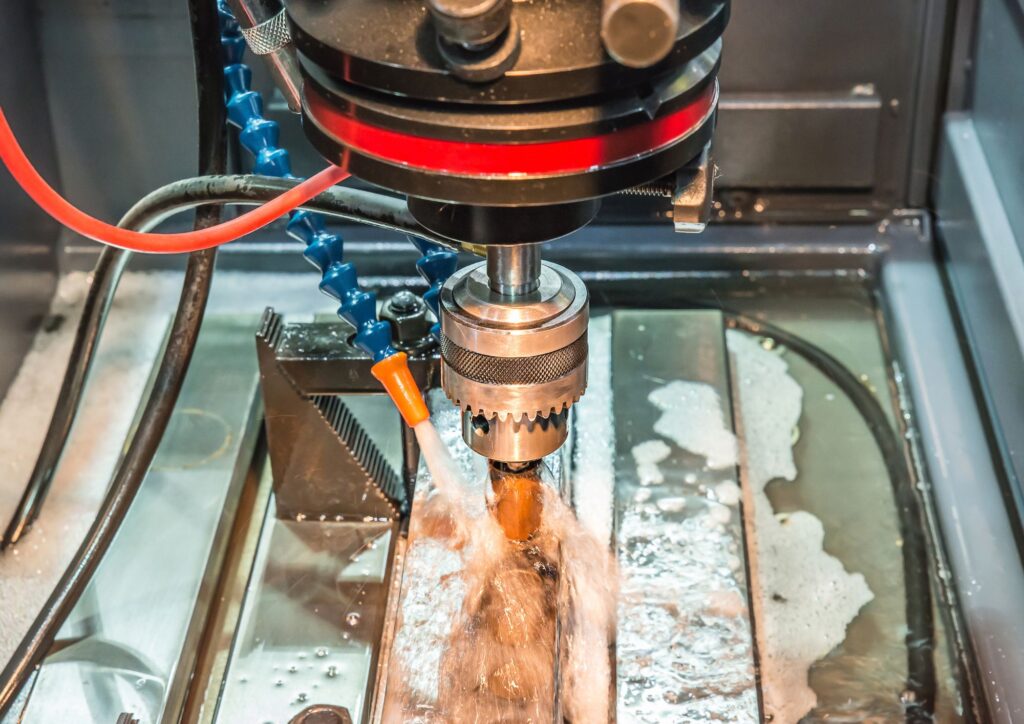
He wire EDM cutting It stands out for its ability to offer extreme precision, work with a wide range of materials and minimize thermal deformations. These qualities make it a preferred solution compared to methods where quality and detail are essential. If your industry requires complex parts or works with difficult materials, this method is a strategic investment that will guarantee superior results.