Wire EDM: What you need to know
The wire EDM is an advanced machining technique that allows for obtaining parts with great precision and exceptional finishes. This process, widely used in the manufacturing industry, is based on the erosion of the material by means of controlled electrical discharges. Below, we will explain in detail what wire EDM is, its applications and the advantages it offers over other machining techniques.
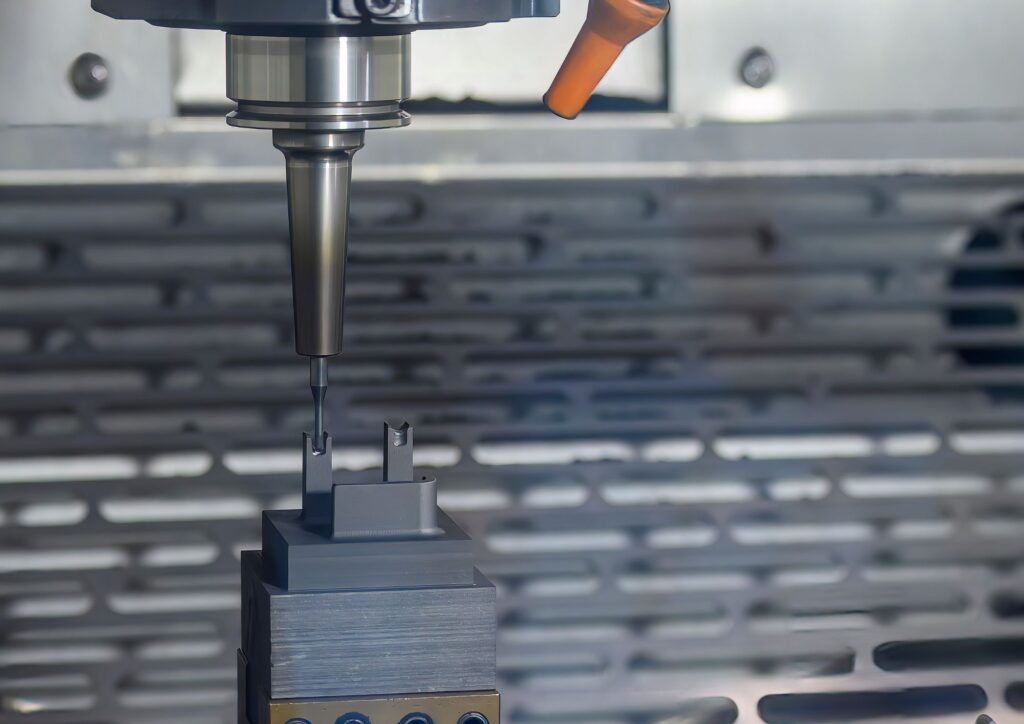
What is Wire EDM?
The wire EDM, also known as EDM (Electrical Discharge Machining), is a non-conventional machining process that uses a conductive wire to cut metal parts. This wire, usually made of brass or copper, acts as an electrode and moves continuously through the material to be machined, while an electric current passes between the wire and the part. The generated electric discharges cause erosion of the material, allowing high-precision cuts to be made.
How the Wire EDM Process Works
The process of wire EDM It is carried out in a dielectric medium, usually deionized water, which acts as an insulator and coolant. The conductive wire, fed by a coil, moves through the piece following the path programmed in a CNC (Computerized Numerical Control) machine. As the wire moves, small sparks are generated that erode the material at specific points. This controlled erosion allows for extremely precise and complex cuts.
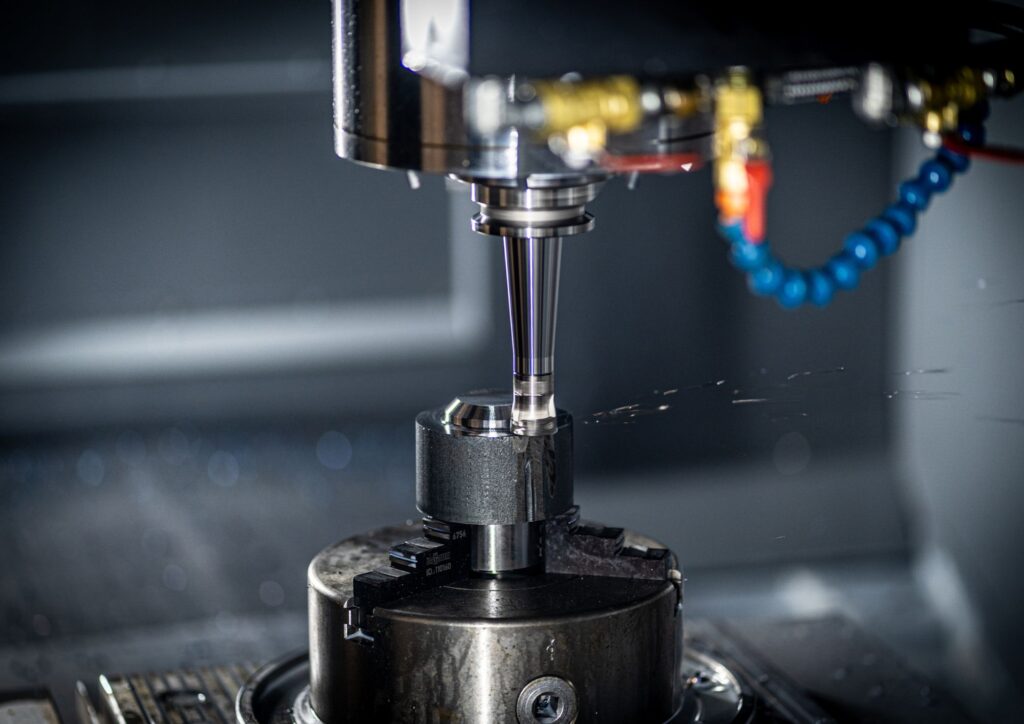
Applications of Wire EDM
The wire EDM It is used in a wide variety of industries due to its ability to work with hard materials and make detailed cuts. Some of its most common applications include:
Aerospace industry
In the aerospace industry, the wire EDM It is used to manufacture critical components for aircraft engines and structures. The ability to cut high-strength alloys with millimetre precision is essential to ensure aircraft reliability and performance.
Manufacturing of molds and dies
The precision of the wire EDM It is essential in the manufacture of moulds and dies used in the production of plastic and metal parts. This process allows for the production of moulds with intricate details and very tight tolerances, improving the quality of the final products.
Medical Industry
In the medical industry, the wire EDM It is used to produce surgical instruments and medical device components. The precision and surface finish that can be achieved are crucial to ensuring the safety and effectiveness of these products.

Advantages of Wire EDM
The wire EDM It offers several advantages that make it preferable in many machining applications:
High Precision and Cutting Quality
The ability to make precise cuts with a high quality surface finish is one of the main advantages of the wire EDMThis allows for complex and detailed parts to be obtained without the need for additional finishing processes.
Work with Hard Materials
Unlike other machining methods, the wire EDM It can work with extremely hard and resistant materials, such as hardened steels, tungsten carbide and titanium alloys. This makes it ideal for applications requiring high-strength components.
Reducing Tool Wear
In the wire EDM, the conductive wire does not come into direct contact with the workpiece, which reduces tool wear and extends equipment life. This also contributes to maintaining process accuracy over time.
In short, the wire EDM It is an advanced machining technique that offers high precision, cutting quality and the ability to work with hard materials. Its applications in industries such as aerospace, mold and die manufacturing, and the medical industry highlight its versatility and effectiveness. Without a doubt, the wire EDM It is an indispensable tool in the field of modern machining.