What are EDMs?
The EDM Electrical discharge machining is a non-conventional machining process that uses controlled electrical discharges to shape hard, conductive materials. This method is ideal for working with metals that are difficult to cut using traditional techniques, such as tungsten carbide and titanium. Electrical discharge machining machines, also known as EDM (Electrical Discharge Machining) machines, use an electrode to generate a series of sparks that erode the material, allowing for the creation of complex, high-precision shapes.
The technology of the EDM EDM is divided into two main types: wire EDM and die sinking EDM. In wire EDM, a fine wire is moved through the material, cutting it with great precision. In die sinking EDM, a shaped electrode is sunk into the material to shape it. Both methods are essential in the manufacture of complex parts that require high accuracy and fine finishes.
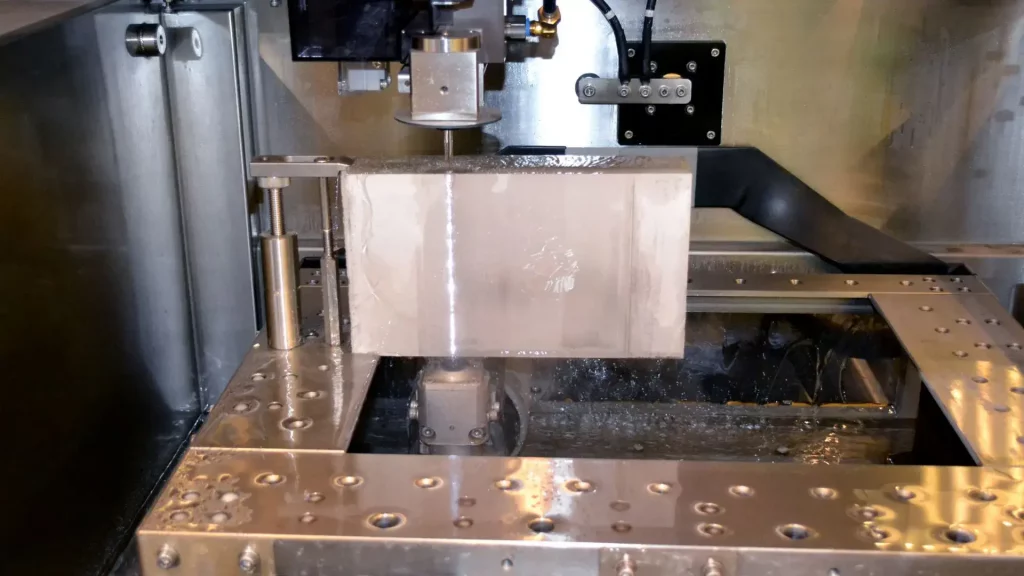
Benefits of EDM
The EDM They offer numerous benefits that make them indispensable in various industries, from automotive to aerospace. Some of the most notable benefits include:
- High Precision and Detail:EDM machines can create parts with extremely tight tolerances and fine detail. This is crucial in mold and die manufacturing, where accuracy is critical to the performance of the final product.
- Versatility of Materials: Unlike other machining methods, EDM They can work with extremely hard and brittle materials. This includes metals such as tungsten carbide, titanium and advanced alloys that are difficult to cut with conventional tools.
- Fine Surface Finishes: Parts produced by EDM have very smooth surfaces, reducing the need for additional finishing processes. This not only saves time, but also improves the quality of the final product.
- Ability to Create Complex Shapes: The EDM They allow the creation of intricate geometries and deep cavities that would be impossible or very difficult to achieve using other machining methods. This is especially useful in the production of components for the medical industry, where precise and complex shapes are required.
- Reduction of mechanical stress: Since there is no direct contact between the electrode and the material, the EDM They reduce the risk of deformation and mechanical stress on the parts, preserving their structural integrity.
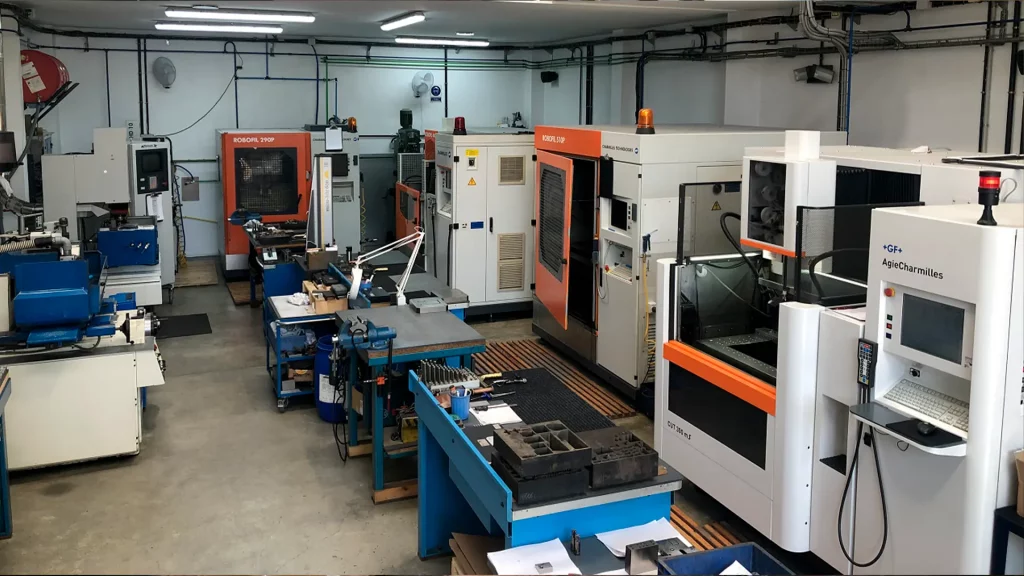
Applications of Electroerosion in Industry
The EDM They are widely used in a variety of industrial applications. In the automotive industry, for example, they are used to manufacture plastic injection moulds and engine components with high precision. In the aerospace industry, they are essential for producing jet engine parts and structural components that must withstand extreme conditions. The medical industry also benefits from the use of EDM for the manufacture of medical devices and prostheses with complex shapes and fine finishes.
In short, the EDM They represent an advanced and efficient solution for machining hard and complex materials. Their ability to produce parts with high precision, versatility in the use of materials and the possibility of creating detailed shapes and fine finishes make them an indispensable technology in modern manufacturing. If you need high quality and precision parts, EDM are the ideal option for your project.
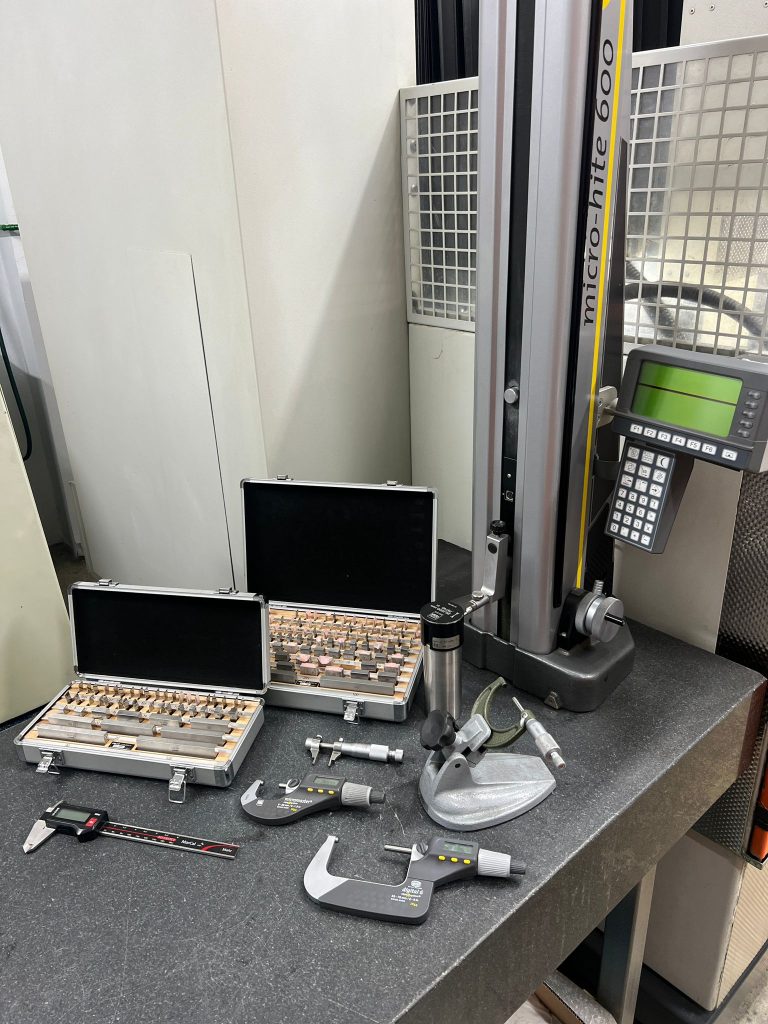